How to do a Quality Control Inspection in China Even When You’re Not There
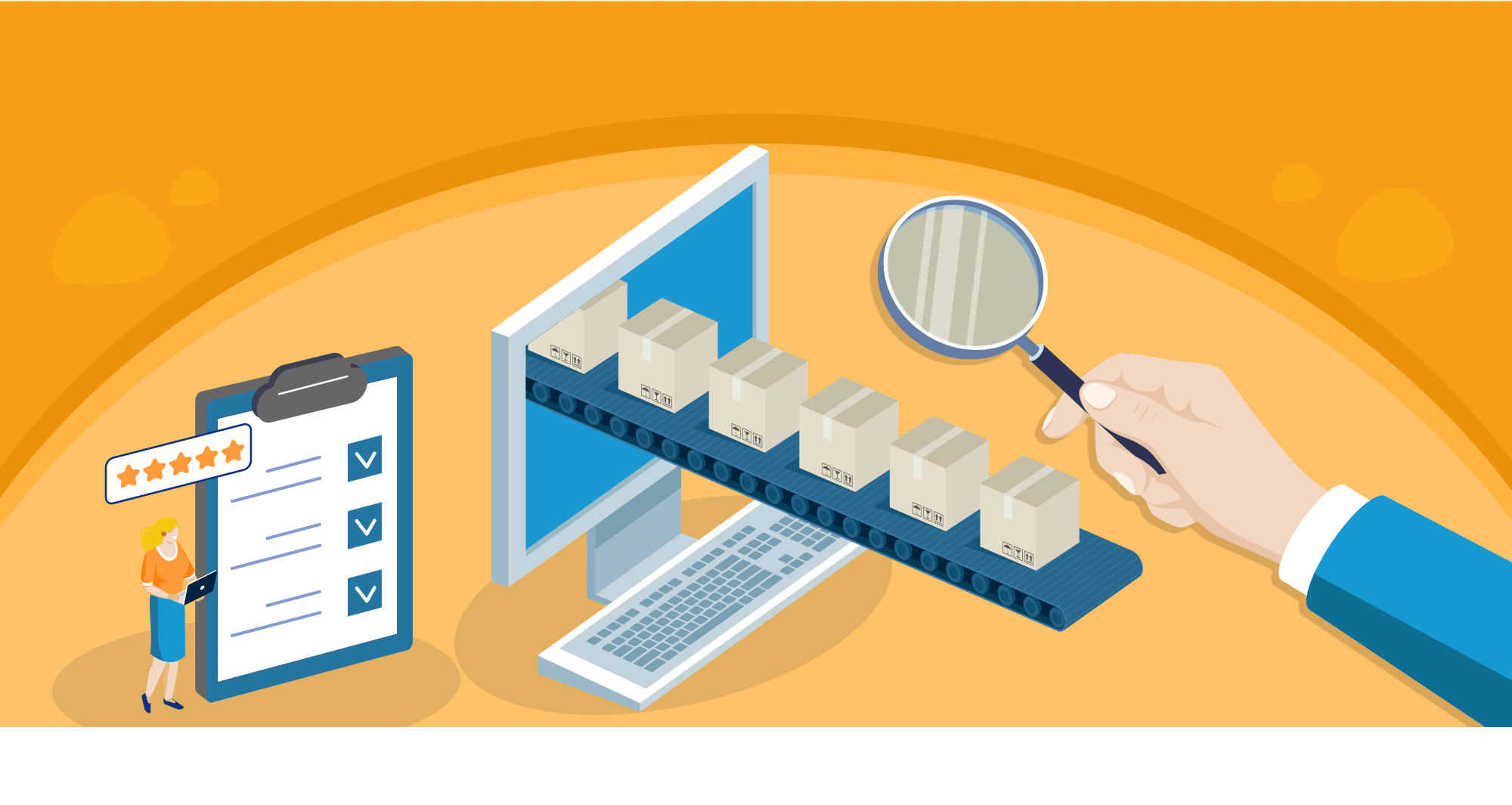
For importers and private labelers, there's only one thing scarier than hearing the words “poor quality products”: It's finding out that your shipment has been rejected by Amazon because it wasn't labeled correctly.
This is why if you're importing anything from China, you should be familiar with quality control inspections. This might sound intimidating and expensive but they're cheap and simple to do. For around $300 for each shipment, you can drastically improve the quality of your products and in turn, sell more products. You can almost entirely eliminate your likelihood of being scammed.
Related Podcast: Episode 276: How to Do Sourcing Right – A Guide for Veterans and Novices
Contents
- How It Works and How Much It Costs
- Pros and Cons of Having a Third-Party Quality Control Inspection
- What Amazon Sellers Need to Inspect For
- Do I Still Need an Inspection?
- How to Do A Pre-Shipment Amazon Inspection: Step-by-Step Instructions
- What Happens If They Do Find Something Wrong During Inspection?
- Conclusion
How It Works and How Much It Costs
A quality control inspection is almost always undertaken by a third-party company. By far the most popular company for inspections is QIMA, previously known as AsiaInspection. This isn't simply because they are our podcast sponsor but also because of their price and reliability.
Inspection companies like QIMA will dispatch a quality inspector in China to your supplier's factory or warehouse and perform an inspection either to your specifications or a default set of specifications. Any of the quality inspection companies can send an inspector anywhere in China.
It's shocking how cheap a third-party inspection is. A typical inspection with QIMA is roughly $300. It's billed on what they call man-day, i.e., what an inspector can perform in 8 hours. And for most situations, you will almost never need more than one man-day. This $300 includes all transportation and other expenses.
Pros and Cons of Having a Third-party Quality Control Inspection
Pros
- Verify your items exist
- Verify that your products are labeled and barcoded
- Verify the number of products is correct
- Inspect product quality
- Inspect product packaging
- Avoid non-deliberate/deliberate and careless mistakes from your supplier
- Verify your shipment before the final payment
- Prevent all the future risks
- Suppliers will take your orders more seriously
- Improve your brand's reputation, which may increase sales
Cons
- Extra expense
What Amazon Sellers Need to Inspect For
You can do very complicated inspections and testing like testing lead content, doing tensile strength tests, etc. However, for me (and probably the vast majority of other private labelers), I simply book what they call a Pre-Shipment Inspection and make the following requests:
- See and verify that my shipment actually exists and I am paying for what I ordered
- Verify if the items are labeled and barcoded correctly (so they don't get rejected by Amazon)
- Count my items to ensure I am getting the exact number of pieces I ordered
- Do some very basic product quality verification, e.g., make sure the items are visually in perfect condition, make sure that the blue jeans I ordered are blue and not red
The truth is that most Amazon sellers primarily want to inspect for quantity verification, barcoding and packaging, and to do some very basic visual confirmation that the products they're ordering look as they would expect. In most cases, you don't know what else to test for until something goes wrong.
I Completely Trust My Supplier. Do I Still Need an Inspection?
There are a few reasons to do a third-party inspection:
- To avoid non-deliberate and careless mistakes from your supplier
- To avoid deliberate mistakes from your supplier
- Verify your shipment before final payment
The vast majority of issues happen because of non-deliberate mistakes from your supplier. Such mistakes I've experienced are things like barcoding items incorrectly, putting Amazon carton labels on the inner cartons (i.e., inside) instead of on the outside, putting items in the wrong box, putting multiple items in one inner box to save space, and the list goes on. These aren't things your supplier is doing to be malicious. They're simply careless mistakes that happen for a variety of reasons. A third-party inspection removes almost all the risk of these types of things happening.
Deliberate mistakes are harder to test for. You have to know your product inside-out in order to test for it. The most common type of deliberate mistake is the substitution for inferior materials. In fact, suppliers don't view this as malicious. For example, if you didn't specify 600D polyester fabric in your Purchase Order, then they will think it is perfectly acceptable to substitute you for 300D fabric (a fabric roughly half the quality of 600D Polyester).
The last reason to do a third-party inspection is to keep your supplier on their toes. If they know a third-party inspection is coming, or they know that you have a habit of conducting third-party inspections, they'll be less likely to cut corners and take more care with your products. There are a lot of companies that never do third-party inspections. If your supplier knows that you are a company that does inspections, whose order do you think they're going to be more careful with?
Finally, if you're on 30/70 payment terms (70% due upon shipment completion) having a third-party inspector seeing your shipment, live in the flesh, before paying your final payment gives a lot of reassurance that you're going to get your goods.
How to Do A Pre-Shipment Amazon Inspection: Step-by-Step Instructions
The following guide is based on the QIMA interface. The principles remain the same whether you use them or not.
Step 1: Gather What You Need
You will need just a couple of things to start:
- Your purchase order with your supplier (or at least a list of the items on the order)
- Your supplier's contact information, so QIMA can contact them to make an appointment
Step 2: Inform Your Supplier as Soon as Possible That You Will Be Doing a Pre-Shipment Inspection
Once you place your order with your supplier, inform them that you will be performing a pre-shipment inspection. If your order is already in production, that is fine too. But tell them as soon as possible about the inspection. In either case, ask your supplier to email you a few days before the order will be complete. Once they inform you that your order is almost complete, then book the inspection through QIMA. QIMA should only need a couple of days to arrange the inspection, but by giving everyone as much notice as possible, you avoid any delays.
Step 3: Sign Up for a QIMA Account
Go to qima.com and click “Create New Account.”
When you enter your company name add NS- before it, e.g., NS-ABC COMPANY.
When you add the NS- before your company name you will be given a dedicated account rep who works with us at EcomCrew (either Dory Lanenter or Tracy Balatbat) and who understands the requirements of Amazon/ecommerce sellers.
You can make other specifications as well, but this will ensure your order conforms to best practices for individuals selling on Amazon. This inspection will result in the following (along with other default inspection procedures)
- Verify items are labeled and barcoded correctly (including Amazon Carton Labels if applicable)
- Count your items to ensure they match your Purchase Order quantity
- Do some very basic product quality verification
- Ensure only one day is used and you are not billed for multiple days without your approval
You'll just need to fill in your name, email, and a couple of other details (no payment is required until you book your inspection).
Step 4: Book a Pre-Shipment Inspection
Once you're in your account, you want to book a Pre-Shipment Inspection. There are many types of testing, but this is the one that is most relevant to Amazon and ecommerce sellers.
Step 5: Fill in Your Supplier Details and Inspection Date
In the next step, fill in the estimated time of your inspection and your supplier details. As long as you provide a working email and/or phone number for your Supplier, it is acceptable if the inspection date and/or contact information is incomplete. The inspector and the supplier will arrange a meetup time and directions privately.
Step 6: Add Your Products
On the next page, simply add the product(s) that you are inspecting (just give the product a brief description or use your SKU) and then select a product category (pick whatever category is closest – you don't need to be exact). The other items under Product Specifications you can ignore. You should also upload your Purchase Order at the bottom of the page under File Attachment.
Step 7: Inspection Details
The next page you can more or less ignore. If you had specific tests you wanted to be done, you would describe them here. However, because you signed up following the instructions above, you will have the Amazon specification tests done we mentioned above.
Click next and you're almost done.
Step 8: Payment and Finalization
On the final page, you'll be brought to the payment page. Once you've made the payment, your account manager will reach out to you within a day or two and get to work on your inspection.
Congratulations – you just spent the best $309 you could ever spend in your importing business.
What Happens If They Do Find Something Wrong During Inspection?
For minor problems, e.g., slight scratches, if they are found in 2.5% or less of the goods, it's common practice to just ignore them. You can't expect every product to be perfect anyway. In these cases, you can ask for a discount from the factory, or if you really want to, ask them to correct the items.
However, for major defects, you shouldn't have to pay for the items. In this case, you can ask for corrections, and you may have to do another inspection to make sure that the products are correct this time around. The natural next question would be “Who will pay for the re-inspection?” That's totally up to you. You can ask for the manufacturing company to pay for it, but it's best to have this specified in the purchase order (who pays in case of re-inspection) to avoid an uncomfortable situation.
Conclusion
Now you have an idea of what inspections are, how they are conducted, and the pros and cons of having one.
Ensuring that your products are inspected to verify that quality requirements and specifications are being met will lead you to work more effectively with your manufacturer (since they will take your instructions more seriously) and will help you to keep your customers closer and satisfied. In addition to taking away a lot of headaches, having an inspection quality control service will help you reduce production costs.
Have you ever used Quality Inspection Control for your products? Let us know your experiences with this service in the comments section down below.
except Qima, anyone been worked with AQI Service (https://aqiservice.com)?
AQI Service works great for Amazon FBA Inspection
What % of the product does the inspection agency generally audit ?
Nice Post! thanks for share in quality inspection
What if you are importing and NOT reselling on Amazon? We import for end user, 100% bespoke products. Do you have a link we can go to for this, please?
QIMA works great for Amazon or not for Amazon.
Asia inspection are a great service! Interesting tip about the NS for account mgr assigning. Can that be done in retrospect I wonder…
My main concern is always that it is really hard to know that a lower quality material wasn’t substituted in as you say. I guess that’s were pre prod inspections add benefit.
I have a clause in my sales agreement that states that any re inspections for major issues are at the manufacturers expense. I think this is essential ! :-)
What you can do is ask for a materials invoice for the materials they used in production. This at least proves they purchased the materials. MOST suppliers won’t be outright fraudulent.
As I am just beginning to sell on Amazon, this information is so very valuable. Thanks and keep on going with your excellent content, I am learning so much from you guys.
Glad we can help Risto!
your explanation of why it is useful order for the inspection, how to order for it etc is perfect, I think something is missing to explain : what happens if something is wrong with the inspection? Does the factory correct it? the inspection goes again without charge? How is it?
If only minor problems (i.e. scratches, pulled threads, etc) are found in 2.5% or less of the goods then it’s common practice to just ignore it. More and the factory should either correct or discount. Major defects shouldn’t be paid for. For the re-inspection, that’s up to you if you want to push the factory to pay for it or not but this should have been specified in the PO to begin with (who pays in the case of re-inspection) to avoid that uncomfortable situation.
More and more sellers realized that pre-shipment inspection can’t ignore during their importing process, that’s true!
Have you had to submit an Alibaba Trade Assurance claim yet? If so, what was your experience?
Never. Are you having to file a claim or are you asking for curiosity’s sake?